First, the pump is not water Analysis of the cause of the air inlet pipe and the pump body (1) before the pump is not fully filled with water, sometimes it seems that the irrigation water has overflowed from the vent hole, but did not turn the pump shaft air completely discharged, resulting in A little air remains in the inlet pipe or in the pump body. (2) The horizontal section of the inlet pipe in contact with the pump applies a descending gradient of 0.5% or more to the direction of the flow of water, and the one end connected to the inlet of the pump is the highest, not to the full level. If you tilt up, there will be trapped air inlet pipe, reducing the vacuum hose and pump, affecting water absorption. (3) The packing of the pump is worn or the packing pressure is too loose due to the long-term use, resulting in a large amount of water being ejected from the gap between the packing and the shaft sleeve of the pump. As a result, external air enters the pump from these gaps, Affected the mention of water. (4) Inlet pipe Due to long-term potential underwater, pipe wall corrosion holes, water pumps continue to decline after work, when these holes exposed water, the air from the hole into the civilian into the water pipe. (5) cracks in the inlet pipe cracks, inlet pipe and pump connections appear tiny gaps, are likely to make the air into the inlet pipe. Second, the pump speed is low (1) human factors. Some users due to the original motor damage, it is coupled with another motor driven, the result of a small flow, low lift or even the consequences of the water. (2) the pump itself mechanical failure. Loosening of the impeller and the shaft of the pump shaft or the deformation and bending of the shaft of the pump cause the impeller to move more, friction directly with the pump body or damage to the bearing, all of which may reduce the speed of the pump. (3) power machine repair is not working. Motor due to the winding burned, and loss of magnetism, the maintenance of the winding turns, diameter, connection method changes, or maintenance failure is not completely ruled out factors also make the pump speed change. Third, the pump suction too deep Some of the water is deep, some of the water's outer periphery is relatively flat, while ignoring the allowable suction pump, which resulted in less water or simply can not absorb the results of the water. To know the pump suction port can establish a degree of vacuum is limited, the absolute vacuum suction is about 10 meters high water column, and the pump can not establish an absolute vacuum. And the vacuum is too large, easy to pump the water gasification, the work of the pump negative. Therefore, the centrifugal pump has its maximum allowable suction, usually between 3-8.5 meters. Do not install the pump only easy and simple. Fourth, the flow of water out of the resistance loss is too large Some users after the measurement, although the vertical distance from the reservoir or water tower to the water surface is slightly less than the head of the pump, but still mention the amount of water is small or mention the water. The reason is often too long pipes, pipe corners, water flow resistance in the pipeline is too large loss. The reason is often too long pipes, pipe corners, water flow resistance in the pipeline is too large loss. Under normal circumstances, 90-degree elbow bend than the 120-degree bend resistance, each 90-degree elbow head loss of about 0.5-1 meters, 20 meters of pipe resistance can make head loss of about 1 meter. In addition, some users are also free to pump into and out of the pipe diameter, which also has a certain impact on the lift. $$ Div $$ Fifth, the impact of other factors (1) at the end of valve does not open. It is usually due to the pump being left on for too long, the bottom valve gasket is stuck, and the bottom valve without gasket may rust out. (2) The bottom valve filter screen is clogged; or the bottom valve causes potential clogging of the filter screen in the sludge layer. (3) impeller wear serious. Impeller blades worn by long-term use, affecting the pump performance. (4) Gate valve can check valve failure or blockage will result in reduced flow or even pumping on the water. (5) Leakage of the outlet pipe will also affect the amount of water lift. Sixth, commonly used simple equipment fault diagnosis methods Commonly used simple state monitoring methods are auscultation method, touch method and observation method. 1, auscultation method equipment normal operation, accompanied by the sound always has a certain temperament and rhythm. As long as you are familiar with and master these normal rhythms and rhythms, you can compare whether the equipment has abnormal noise, miscellaneous noise, oddness or chaos through the human auditory function and judge the loosening, impact and unbalance in the equipment. Tap the parts with a hand hammer, listen to the occurrence of cracked noise, can determine whether there is a crack. Electronic stethoscope is a vibration acceleration sensor. It converts the vibrations of the equipment into electrical signals and amplifies them, and the worker monitors the vibration of the operating equipment with headphones to achieve qualitative measurements of the sound. By measuring the same measuring point, different periods, the same speed, the same signal conditions, and compared to determine whether the device is faulty. When the headset appears crisp and sharp noise, indicating a higher vibration frequency, the size is generally relatively small, relatively high strength parts localized defects or micro-cracks. When the headphone emits a cloudy, low noise, it indicates that the vibration frequency is low, and generally a relatively large size and a relatively large strength crack or defect occurs in a relatively low-strength part. When the noise coming from the earphone is stronger than usual, it shows that the fault is developing. The bigger the sound is, the more serious the fault is. When the noise comes from the headphones is intermittent irregular chaos appears, indicating that parts or components have been loose. 2, touch method touch with the manpower can monitor equipment temperature, vibration and gap changes. Nerve fibers on the hands of the more sensitive to temperature, you can more accurately distinguish the temperature within 80 ℃. When the temperature of the parts is about 0 ℃, feel cold, if the touch for a long time will produce biting pain. About 10 ℃, feel cooler, but generally tolerate. About 20 ℃, feel cooler, with extended contact time, feel warm. About 30 ℃, feel warm, comfortable. 40 ℃ or so, feel hot, slightly hot feeling. About 50 ℃, feel hot, if the palm press for a long time, there will be sweat. About 60 ℃, feel very hot, but generally can tolerate 10s long time. About 70 ℃, feel hot burning, the general can only endure 3s long time, and the hand touch will quickly turn red. When touched, touch it and touch it carefully to estimate the temperature rise of the part. Rocking the mechanism by hand can feel the gap size of 0.1mm-0.3mm. Touch the device can feel the vibration of the changes in the intensity and whether the impact, as well as the slide board crawling situation. Using a thermometer equipped with a surface thermocouple probe to measure the surface temperature of a rolling bearing, a sliding bearing, a spindle box, a motor and the like, the invention has the advantages of promptly determining the location of the thermal anomaly, accurate data and convenient touch detection process. 3, the observation of corporate vision can observe the mechanical loosening of the device, cracks and other injuries; can check the lubrication is normal, with or without dry friction and run, run, drip, leakage phenomenon; can view the metal deposits in the sediment How many grains, size and characteristics of the parts to determine the wear and tear of related parts; can monitor equipment movement is normal, with or without anomalies; can watch the installation of the equipment to reflect the working conditions of the instrument to understand the changes in the data, Through the measurement tools and direct observation of surface conditions, testing product quality, to determine the working conditions of equipment. The observation of a variety of information for a comprehensive analysis, can the existence of equipment failure, fault location, the extent of the fault and the reasons for failure to make judgments. A simple method of observing the wear particles collected from the equipment's lubricant through the instrument is the magnetic plug method. Its principle is to insert the magnetic plug into the lubricating oil to collect the iron particles produced by wear and tear, with the help of reading microscope or directly observe the size, quantity and shape characteristics of the abrasive particles to judge the wear of the mechanical parts degree. With the magnetic plug method can be observed at the late wear of mechanical parts abrasive particle size larger situation. Observation, if found a small number of small particles, indicating that the normal operation of the device; if the discovery of large particles, it is necessary to pay attention to the operation of the device closely; if the continuous discovery of large particles, is imminent failure The precursor, should immediately stop checking, find fault, to be ruled out. Speaking in great detail, these diagnostic methods require a longer period of accumulated experience in order to judge accurately. [Supplementary] Auscultation can be used to change the tip of the tip (or metal rod) aligned to the diagnosis of the site, with a screwdriver handle, put the ear to listen. This can filter out some noise. Temperature feel judgment training: With a knot-point thermometer to measure the metal surface of 50 degrees, 60 degrees, 70 degrees, 80 degrees of several states, for low temperature can be used to describe the hand can contact time, according to different time Determine the temperature. When the temperature can not touch the higher temperature, you can pour a small amount of water droplets observed water evaporation, and then remember these conditions. Used in the diagnosis of equipment, can get more accurate judgments. I feel temperature feel in the "modern mechanical and electrical equipment installation commissioning, operation detection and troubleshooting, maintenance management practices book" book, but I think everyone's tolerance may vary, or with the total moderator said Method to judge their own more accurate. $$ Div $$ Troubleshooting of the pump trip 1: Symptom The 125 mw unit of the power plant has been tripped since it was put into production. There is no sign-off of any signal relay. After excluding the switchgear failure, according to the conventional method of checking the cable, the secondary circuit wiring and the relay and its rating are normal, start again often successful. Dcs system after the suspicion of soft failure caused, but the change in the control panel operation, there will still be this phenomenon. 2: The reason for the test to find out the reasons for this phenomenon, observe the changes in the process of closing the switch to confirm what is the reason for tripping. Test voltage meter which monitors the microcomputer trip circuit, mA watch differential relay 1cj, 2cj action, ammeter monitoring thermal protection circuit. Pick up a good meter, start to the pump, after a period of testing, and finally once the pump started that trip, while observing the mA ammeter deflection of the watch a bit, the other watch does not respond, the new xjl- 0025/31 integrated block signal relay 1xj also action card, that is caused by the differential protection action trip. 3: Root Cause Analysis of differential protection, first of all suspected to be protected equipment within the fault. Through routine inspection, the pump motor and its cables are normal, the differential relay is calibrated, and the polarity of the current transformer is connected correctly. After eliminating the causes of equipment failure and wiring errors, differential protection operates during motor start-up, indicating that the differential current of the differential circuit exceeded the differential relay setting during this process. Under normal circumstances, the differential current caused by differential current loop there are two main reasons: First, both sides of the motor current transformer ratio error is different, there is a small difference current, the difference current is less than 5% of the motor rated current id . Second, both ends of the current transformer secondary load difference will cause the difference between the ratio, so there is a difference current. The difference of the current transformer load in the differential protection circuit of the pump motor is only the difference of the length of the secondary cable, about 50 m, and the power consumption of the differential relay is not more than 3 va at rated current, the secondary load is not heavy . Check found to pump motor differential protection with the end of the current transformer models are lmzbj-10, b-level 15 times the rated current, the ratio of 600/5, the capacity of 40 va, fully able to meet the requirements of the secondary load. The above analysis is based on the normal operation of the condition, the motor starts, the situation is different. When the motor starts, the current is very large. The current transformer on both sides of the motor may be saturated. In this case, the secondary differential current may be very large due to the inconsistent magnetization characteristics of the current transformers. According to Acheng Relay Factory lcd-12 differential relay setting instructions, the relay operating current setting izd = △ i1 × kk × in / n = 0.06 × 3 × 356/120 = 0.53
Differential Bearing
Deep Groove Ball Bearings
Deep groove ball bearings The out looks of them are nearly the same,the only different is the size,you may need other models please check the following table for reference.are the most widely used bearing type and are particularly versatile.
They have low friction and are optimized for low noise and low vibration which enables high rotational speeds.
They accommodate radial and axial loads in both directions, are easy to mount, and require less maintenance than other bearing types.
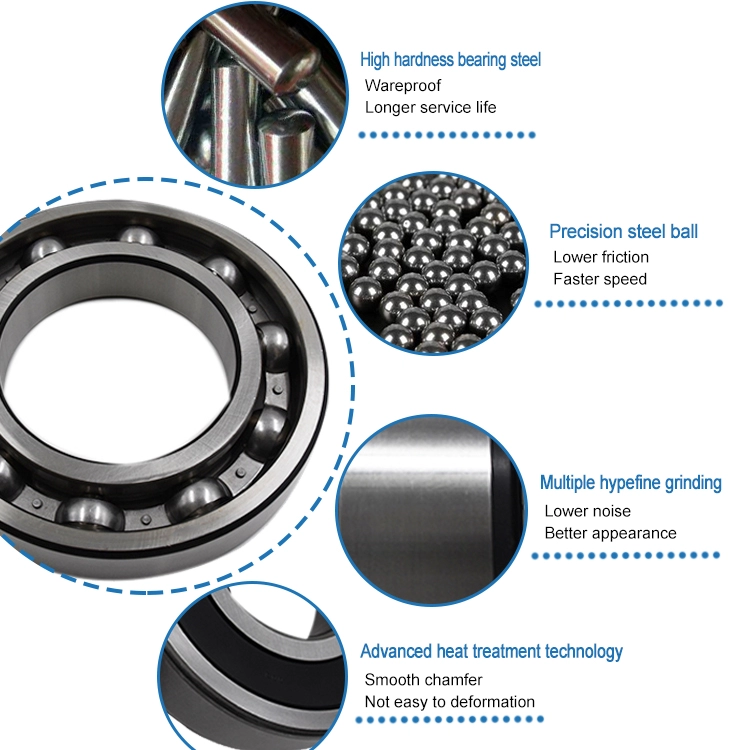
Deep groove ball bearings are divided into the following series: 6000series, 6100series, 6200series, 6300series, 6400 series, 6700 series, 6800 series,6900 series,16000 series etc.
Model
|
d(mm)
|
D(mm)
|
B(mm)
|
6000ZZ
|
10
|
26
|
8
|
6001ZZ
|
12
|
28
|
8
|
6002ZZ
|
15
|
32
|
9
|
6003ZZ
|
17
|
35
|
10
|
6004ZZ
|
20
|
42
|
12
|
6005ZZ
|
25
|
47
|
12
|
6006ZZ
|
30
|
55
|
13
|
6007ZZ
|
35
|
62
|
14
|
6008ZZ
|
40
|
68
|
15
|
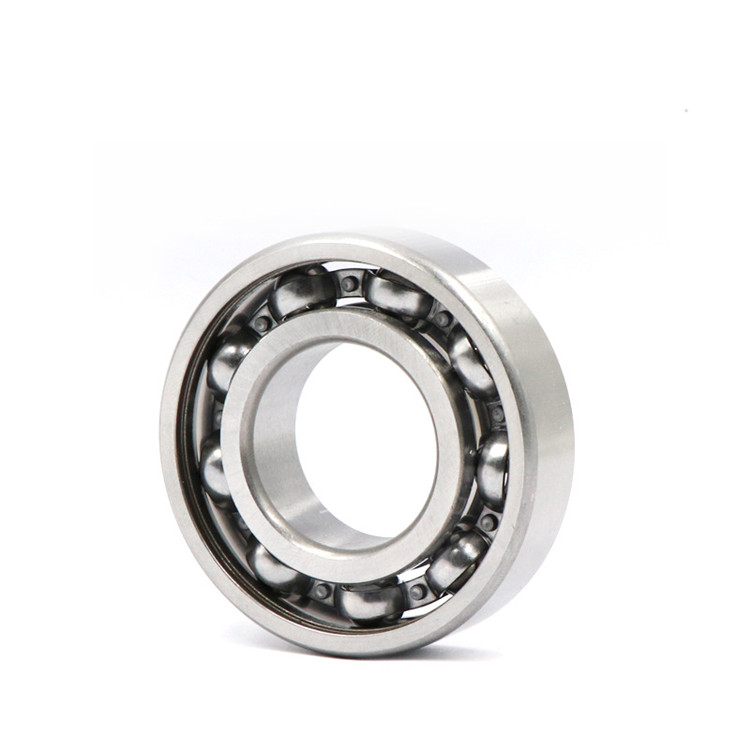
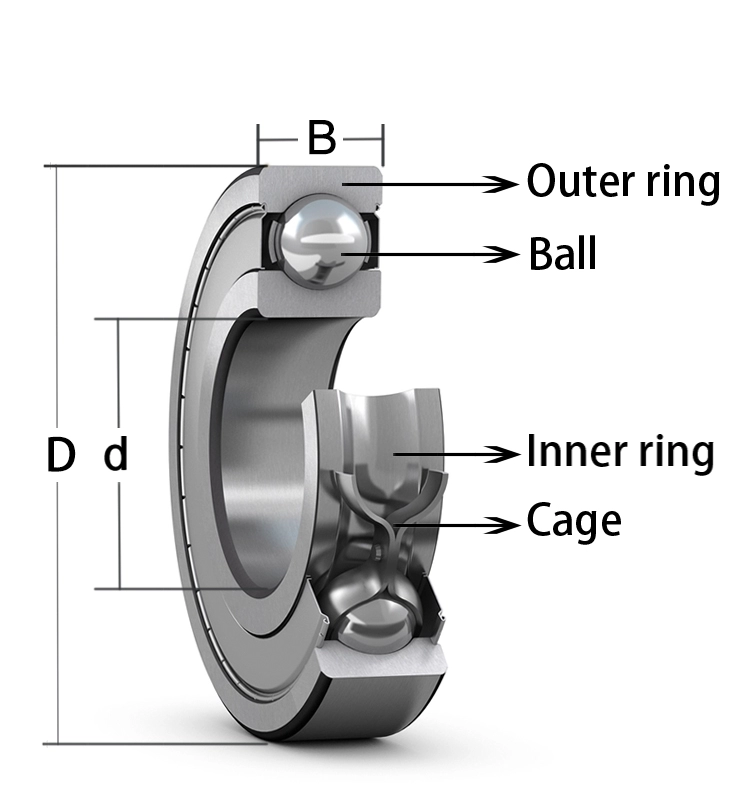
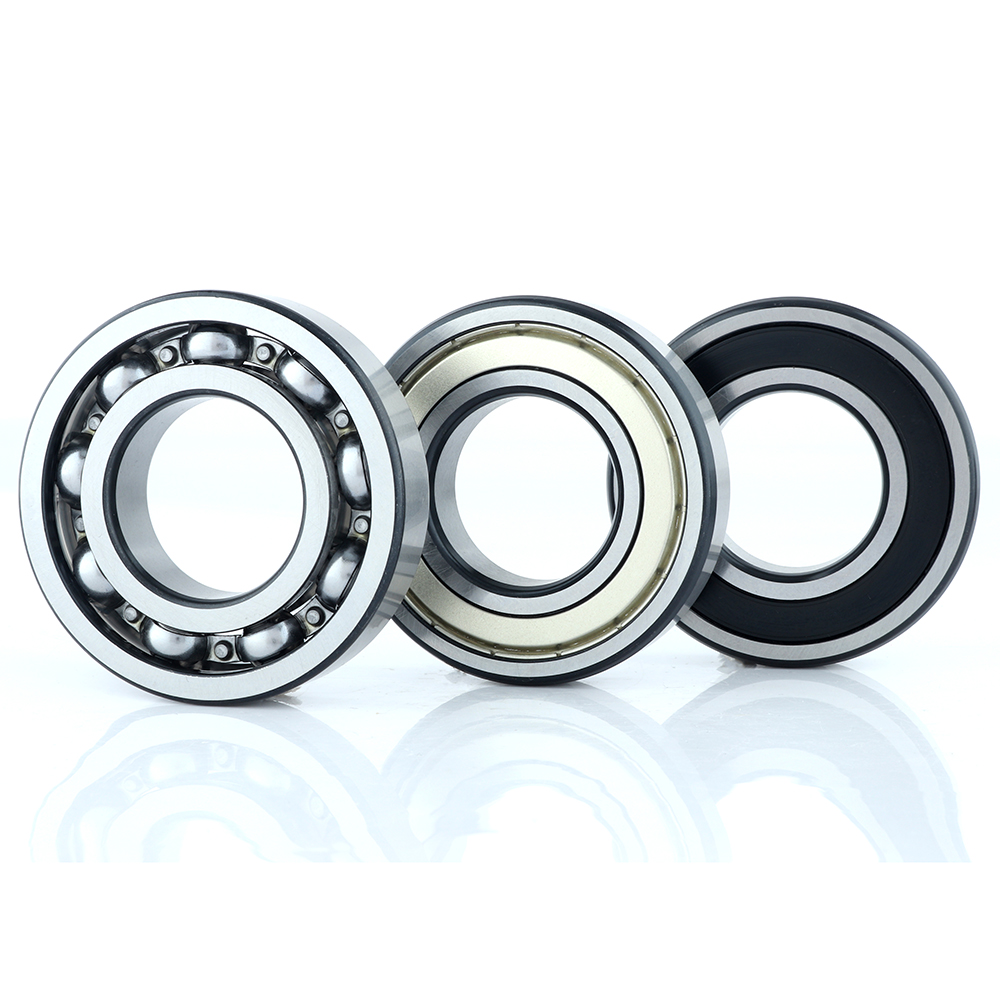
We manage in all kinds of ball bearings and roller bearings,such as
1.Deep Groove Ball Bearing
2.Self-aligning Ball Bearing
3.Cylindrical Roller Bearing
4.Spherical Contact Bearing
5.Angular Contact Bearing
6.Tapered Roller Bearing
7.Thrust Ball Bearing
8.Insert Bearing
Package
1.Small bearings|:plastic tube+carton+pallet
2.Medium bearings:PE bag+box+carton+pallet
3.Large bearings:PE film & paper winding+carton+pallet
4.According to the customer's requirements
High Ball Bearing,Miniature Ball Bearing,Deep Groove Ball Bearing,Deep Ball Bearing
Shijiazhuang Longshu Mechanical & Electrical Equipment Trading Co., Ltd. , https://www.longsbearing.com