Abstract Hard turning is defined as the machining process for single point cutting of workpieces with hardness above HRC45. As an application field, it has been the focus of tool development. With the emergence of various high-hardness complex materials, hard turning has not been limited to gear steel after heat treatment...
Hard turning is defined as the machining process for single point cutting of workpieces with a hardness of more than HRC 45. As an application field, it has always been the focus of tool development. With the appearance of various high-hardness and complex materials, hard turning is not limited to the processing of hardened parts such as gear steel, bearing steel and die steel after heat treatment, and also applies thermal spray welding materials and chrome-nickel alloy and heat-resistant nickel. Base alloy, stellite cobalt alloy material processing. At present, PCBN tool is the field of ferrous metal processing, and it is the tool material with the highest wear resistance. After demonstration, its life is generally several times to several times that of cemented carbide blades and ceramic blades. PCBN tool is the pioneer of localization and wins. In the innovation and improvement of tool material grades, such as the PCBN tool grade BN-K10 developed by Valin HLCBN, it can process tungsten carbide with hardness above HRC70, which is the first case in China; this grade tool is also widely used in mining machinery industry. Hard-wearing for wear-resistant castings and rolling mills, hard turning of high-hardness pump parts such as high-chromium alloy cast iron impellers. Compared with the grinding process, the use of hard turning reduces the capital investment of machine tools and equipment, and enables flexible production and efficient use of equipment. In terms of processing quality, 80% of the heat generated by hard turning The chips are taken away, so the grinding burns are reduced. In terms of processing efficiency, the machining efficiency of hard turning by car grinding is 4-6 times of grinding; and the hard turning chips are easier to recycle.
Hard turning is the final machining or finishing process to completely avoid grinding and its risks. The machine tool clearance and rigidity used in hard cars and the performance and precision of each moving shaft integration, including machine tool accuracy, geometric accuracy, and electronic control functions. , error compensation and general adjustment and thermal deformation effects, which determine the probability of the knife and the knife problem in the hard turning process, and also affect the dimensional accuracy and shape tolerance of the machined workpiece, so when using hard turning completely Instead of precision grinding to complete the final size, it needs to be considered according to the requirements of its own workpiece. For some workpieces with ultra-high precision requirements and special requirements, especially when it is limited by the precision and rigidity of hard machine tools, the grinding process is still compared. The right choice.
Although hard turning is not a complete replacement for ultra-high precision grinding, it has been able to replace a considerable portion of precision grinding, thereby reducing the costly production costs of the grinding manufacturing process. The typical case where the hard turning process completely replaces the grinding to achieve the final machining is the processing of hardened steel gears by Valin BN-H20 (Fig. 1). The surface roughness of the gears after hard turning reaches Ra0.4 (equivalent to Rz3.2). . Fully meet the requirements of gear grinding.
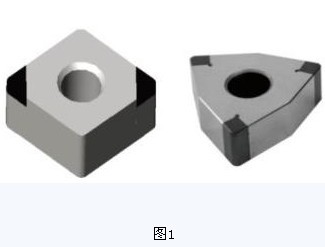
BN-H20 and BN-H10 grades are typical PCBN tool grades for finishing hardened parts. In addition to standard CNC inserts, non-standard boring tools, grooving cutters and other forming turning tools can be ordered, as shown in Figure 2.
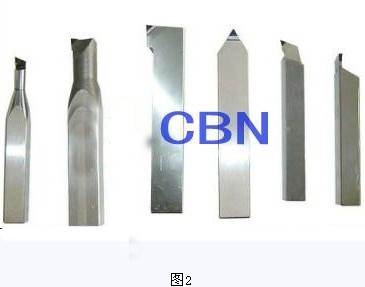
The term "cars for grinding" has been used for a long time, but PCBN blades for hard turning are often used in finishing. When the hardness of the workpiece is high and the machining allowance is large, the traditional process is generally followed by annealing and then cutting, or using a large amount of grinding, the performance of Valin BN-S20 grade PCBN tool fully meets the amount of about 10mm. Hard turning. BN-S20 grade is Hualing super hard CBN sintered body with pure ceramic as bonding agent. It has better impact resistance after high temperature and high pressure synthesis. It avoids the softening of metal bond under high temperature condition by using ceramic as binder. Therefore, the BN-S20 grade is superior in high-temperature wear resistance to the overall PCBN insert of the metal adhesive. Especially in the hard turning of large knife, the life is more than 4 times that of the metal-based bond PCBN blade. At the 2007 BN-S20 product launch conference, the PCBN tool of the super-hard tool industry was broken and could not be used for strong intermittent roughing. The myth of hard materials has caused a lot of sensation in the knives academic world. At present, with Hualing's research progress on CBN tool for ceramic bond, the wear resistance of the tool is increased on the basis of retaining the impact fracture toughness of the tool, which is manifested in the traditional annealing when the hard material is processed. The process and the secondary quenching process solve the difficulty of grinding the large amount of grinding wheel. When used to repair the mold and hard-turn large shaft and disc parts, the BN-S20 grade tool can realize 1 or 2 times. The second pass completes the processing of large margins to improve processing efficiency and processing quality. BN-S20 grades can also be used to process austenitic stainless steel (45HRC), high temperature alloy steel, high manganese steel, high strength steel and high nickel alloy steel, high chromium steel and surfacing materials with poor surface finish quality.
At present, many tools developed in China have been properly processed due to comprehensive factors such as tool materials, structural improvement and manufacturing technology breakthroughs, which have improved the overall level of tool manufacturing in China. PCBN tools are the pioneers of localization and win over tool materials. Innovation and improvement of grades. With the requirements of cost reduction and efficiency increase in the machinery manufacturing industry, the variety, quantity and capital of imported tools have been reduced as an important measure. It is believed that the types and quantity of tools for localization of tools in China will be more and more.
Steel Cross,Stainless Steel Cross,Corbon Steel Cross,Pipe Fitting Cross
Cangzhou Youlong Pipe Fitting Manufacturing Co., LTD , https://www.youlongpipe.com