As we all know, the noise of the winding machine is caused by vibration, then what is caused by the vibration? In fact, there are four main reasons for the vibration, namely: unbalance, misalignment, mechanical looseness and bearing failure.
1. Unbalanced quality
The so-called imbalance is an abnormal state caused by the misalignment of mass and geometric centerlines. When the winding machine main shaft rotates, its "center of gravity" produces a centrifugal force acting on the bearing, and the magnitude of the force changes steadily as the main shaft rotates. There are three types of imbalance: static imbalance or force imbalance, moment imbalance or even imbalance and dynamic imbalance.
The appearance of the spectrum when the main shaft of the transformer winding machine is unbalanced: the waveform is a sine wave; the axis trajectory is a circle or an ellipse; the 1X frequency is dominant; the radial (horizontal and vertical) vibration is dominant; the amplitude increases with the increase of the rotational speed; The over-critical speed has a formant; the unbalanced horizontal and vertical axial vibrations of the cantilever are large. In addition, eccentricity occurs if the center of rotation of the pulley, gear, bearing or rotor deviates from the geometric centerline.
2. Misalignment
Since each of the company's winding machines is subjected to strict horizontal displacement calibration, the general misalignment will occur on older machines. The centering of the machine is very important because it increases. The rotational force exerts an abnormal stress on the bearing and seal. Misaligned types are: parallel misalignment, angular misalignment, parallelism, and angular misalignment.
Typical misalignment is mainly caused by the following reasons: inaccurate assembly of the original components, such as motors, pumps, etc.; relative position between the original components after installation; movement due to the pressure of the piping system; due to torque Flexible support distortion; machine deformation caused by temperature change; coupling surface is not perpendicular to the axis; because the foundation is too flexible, the machine moves when the bolt is tightened.
In fact, most misalignment cases are combinations of misalignment and parallel misalignment of the axis. The general rule is that the diagnosis should be judged according to the change of the vibration level of the corresponding 2X according to the increase of 1X speed in the axial and vertical (or horizontal) directions.
For gear couplings, the following vibration characteristics are generally considered to exist:
a. Poor alignment causes rotor 2 octave vibration component, the more serious the misalignment, the greater the proportion of 2 octave components
b. The greater the damping inside the coupling, the larger the amplitude of the frequency doubling vibration
c. The amplitude of the generated vibration increases as the speed increases
d. The bending vibration caused by good has the even frequency doubling vibration component of the power frequency 2, 4, 6, 8..., and the bending vibration amplitude of the bearing near the coupling is greater than the bearing amplitude away from the coupling; The vibration has a power frequency of 1, 3, 5, 7 ... and other odd-numbered vibration components, and the bending vibration amplitude of the bearing near the coupling is smaller than the bearing amplitude away from the coupling.
3. Mechanical loosening
Since it is loose, it will produce a very obvious 1X fundamental frequency peak. There are two types of looseness in practice: loose rotation and non-rotational looseness. Bearing wear can cause loose rotation, which in the first detection will detect signs of bearing wear before the bearing loosens. When a sliding bearing has a gap problem, its spectrum shows a very similar feature to the looseness of rotation: a strong 1X harmonic appears. In most cases, the vibration in the vertical direction is higher than the vibration in the horizontal direction. For structural loose (elastic foundation) non-rotating looseness, looseness between the machine and the foundation will cause the 1X vibration in the direction of minimum stiffness to rise, usually in the horizontal direction, and also on the way the machine is installed and laid out.
Looseness may cause other failures of the machine or may be caused by other failures. The wear and deformation of the mechanical components, the misalignment of the shafting, the imbalance, and the like may affect the looseness. Because the vibration caused by looseness is mostly medium-low frequency vibration, generally below 1000 Hz, the vibration frequency is usually the fractional harmonic and higher harmonic of the frequency conversion or frequency conversion.
4. Bearing failure
Classification of bearing faults:
a. Rolling bearings: fatigue spalling, wear, plastic deformation, rust, gluing and cage damage.
b. Bearings: bus alloy loose, bus alloy damage, loose bearing housing and excessive bearing clearance.
Need to form a transformer winding machine http:// has many components, consisting of the spindle system, cable system, fuselage mechanism and accessories. After these systems are properly matched and installed, the winding machine can work normally. When some parts of these systems fail or are abnormal, the winding machine will have abnormal noise and temperature rise, which will affect the normal operation of the winding machine.
The abnormal noise caused by the failure of the spindle system, the main shaft is the power component of the winding machine. It is generally composed of a motor, a brake and a bobbin. When abnormal noise occurs, it should be judged in time whether the type of noise is collision sound or friction sound and shaking. The noise caused by the failure of the spindle motor bearing can be solved by replacing the bearing. The noise caused by the abnormal spacing between the brake and the brake disc is generally the friction sound, and the position of the brake disc can be adjusted. Solve, the standard spacing is between 2-5mm, the parallelism of the winding axis is incorrect, which will cause the equipment to sway and abnormal noise. Pay attention to the three-point concentricity between the spindle motor, the winding shaft and the thimble. The deviation should be adjusted in time.
The abnormal noise caused by the failure of the spindle system, the cable system consists of a stepping motor, a lead screw and a moving rod. The stepping motor has a certain sound (non-noise) during normal operation, and the abnormal noise caused by the cable system is often the device. In the absence of the necessary lubrication, the moving rod reciprocates frequently during the normal operation of the winding machine. The lack of lubrication causes the frictional resistance to increase and abnormal noise occurs. In addition, the parallelism between the timing belt and the synchronous wheel of the stepping motor Not allowed will also cause certain abnormal noise.
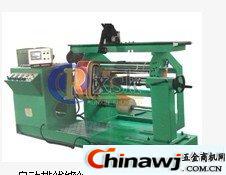
Casing shoes are mostly used for drilling holes in drilling operations. They are useful for fixing when the load is too heavy and difficult to locate in the drilling, which can make the drilling work go smoothly. The human pregnancy casing shoes we produce are suitable for very hard For cracks, loose or broken rock formations, we can produce a full range of casing shoes with standard sizes of carcass hardness and impregnation height to meet the requirements of different customers.
Casing Shoe And Casing Bits,Casing Shoe Bits,Drill Rod Shoe,Casing Shoe
wuxi shengmeirun trading co.,ltd. , https://www.smrxz.com